Distribución en Planta y Manejo de Materiales
Distribución de Planta y Manejo de Materiales
La distribución en planta implica la ordenación de espacios necesarios para movimiento de material, almacenamiento, equipos o líneas de producción, equipos industriales, administración servicios para el personal, entre otros.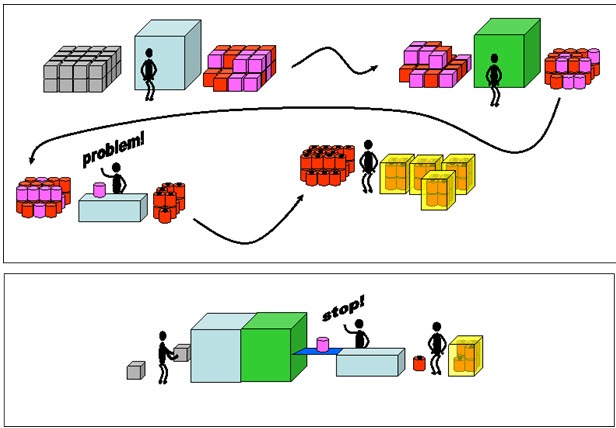
Principios básicos de la distribución en planta
- Principio de la satisfacción y de la seguridad: Siempre será más efectiva la distribución que haga el trabajo más satisfactorio y seguro para los trabajadores.
- Principio de la integración de conjunto: La mejor distribución es la que integra a los hombres, materiales y maquinaria para que resulte mejor el compromiso entre todas las partes.
- Principio de la mínima distancia recorrida: Siempre es mejor que la distancia a recorrer por el material sea la menor posible.
- Principio de la circulación o flujo de materiales: Es mejor ordenar las áreas de trabajo de modo que cada operación esté en el mismo orden o secuencia en que se transforman o tratan los materiales.
- Principio del espacio cúbico: La economía se obtiene utilizando de modo efectivo todo el espacio disponible, tanto en horizontal como en vertical.
- Principio de la flexibilidad: Siempre será más efectiva la distribución que pueda ser ajustada con menos costos.
Tipos de distribución en planta.
- Distribución por posición fija: El material permanece en situación fija y son los hombres y la maquinaria que confluyen hacia él.
- Distribución por proceso: Las operaciones del mismo tipo se realizan dentro del mismo sector.
- Distribución por producto: El material se desplaza de una operación a la siguiente sin solución de continuidad. (Líneas de producción).
·
Materiales.
·
Maquinaria.
·
Trabajadores.
·
Movimientos de personas y materiales.
·
Espera.
·
Servicios.
·
Edificio.
·
Versatilidad,
flexibilidad, expansión.
Manejo de materiales
El manejo de materiales hace referencia al manejo
efectivo de todo material e información utilizando el método correcto para
transportar la cantidad correcta al lugar correcto, en el tiempo requerido, en
la mejor secuencia, en la mejor posición, en la correcta condición y al menor
costo. Además es muy importante tomar en cuenta la calidad, cantidad,
secuencia, orientación, condición, espacio, utilidad seguridad y productividad.
Los principios más importantes que se toman en
cuenta son el planeamiento de producción, flujo de materiales, carga unitaria,
automatización y estandarización de procesos, mantenimiento, sistemas, control,
rendimiento, seguridad, entre otros.
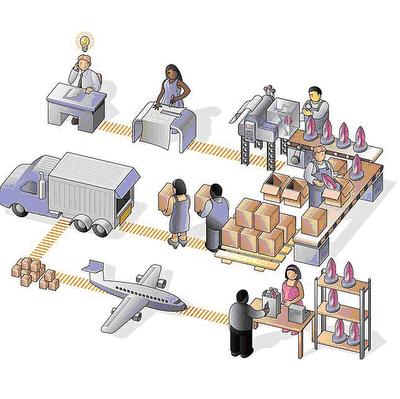
Systematic Handling Analysis (SHA)
El Análisis Sistemático de Manejo (SHA) es un
procedimiento organizado de aplicación al manejo de materiales de cualquier
proyecto, el cual consta de seis procedimientos que se pueden aplicar a
proyectos pequeños que no requieran un análisis profundo del sistema de manejo
de materiales. Los procedimientos que lo componen son:
·
Clasificación
de información.
·
Analizar
la información.
·
Visualizar
el flujo.
·
Establecer
planes.
·
Evaluar
alternativas.
·
Detallar
e instalar.
Se deben examinar los elementos clave de entrada o
información preliminar necesarios para actualizar un problema de manejo de
materiales. Estos son:
·
Productos
o materiales (partes, artículos, unidades).
·
Cantidades
(ventas o volúmenes de contratados).
·
Rutas
(secuencia de operación y requisitos de proceso).
·
Servicio
de soporte.
·
Tiempo.
Sistematic Layout Planning
El
método S.L.P., es una forma organizada para realizar la planeación de una
distribución y está constituida por cuatro fases, en una serie de
procedimientos y símbolos convencionales para identificar, evaluar y visualizar
los elementos y áreas involucradas de la mencionada planeación.
Esta
técnica, incluyendo el método simplificado, puede aplicarse a oficinas,
laboratorios, áreas de servicio, almacén u operaciones manufactureras y es
igualmente aplicable a mayores o menores readaptaciones que existan, nuevos
edificios o en el nuevo sitio de planta planeado.
El
método S.L.P. (Planeación sistemática de la distribución en planta), consiste
en un esqueleto de pasos, un patrón de procedimientos de la Planeación
Sistemática de la Distribución en Planta y un juego de conveniencias.
Como cualquier proyecto de organización,
arranca desde un objetivo inicial establecido hasta la realidad física
instalada, pasa a través de cuatro pasos de plan de organización.
- El paso 1 es el de LOCALIZACIÓN.- Aquí debe decidirse donde va a estar el área que va a ser organizada, este no es necesariamente un problema de nuevo físico. Muy comúnmente es uno de los determinados, si la nueva organización o reorganización es en el mismo lugar que está ahora, en un área de almacenamiento actual que puede estar hecha gratis para el propósito, en un edificio recientemente adquirido o en un tipo similar de un área potencialmente disponible.
- El paso II es donde se PLANEA LA ORGANIZACIÓN GENERAL COMPLETA.- Esta establece el patrón o patrones básicos de flujo para el área de que va a ser organizada. Esto también indica el tamaño, relación y configuración de cada actividad mayor, departamento o área.
- El paso III es la PREPARACIÓN EN DETALLE del plan de organización e incluye planear donde va a ser localizada cada pieza de maquinaria o equipo.
- El paso IV es LA INSTALACIÓN.- Esto envuelve ambas partes, planear la instalación y hacer físicamente los movimientos necesarios. Indica los detalles de la distribución y se realizan los ajustes necesarios conforme se van colocando los equipos.
Comentarios
Publicar un comentario